Certainly! When it comes to CNC machining of aluminum, both the choice of router bits and the types of projects you can undertake are influenced by the characteristics of aluminum as a material. Here’s a breakdown of both aspects:
CNC Router Bits for Aluminum
1.Single Flute End Mills:
2.Advantages: Ideal for aluminum because they have a large flute volume which helps in chip evacuation. They are also sharp and efficient in cutting aluminum.
3.Application: Suitable for cutting aluminum sheets, blocks, and extrusions.
4.Two Flute End Mills:
5.Advantages: Provide good balance between cutting speed and chip removal. They can handle aluminum well, especially softer grades.
6.Application: General purpose milling of aluminum parts and components.
7.Three Flute End Mills:
8.Advantages: Offer higher feed rates than two flute end mills. They provide good surface finish and can handle deeper cuts in aluminum.
9.Application: Used for high-speed machining of aluminum to achieve smoother finishes.
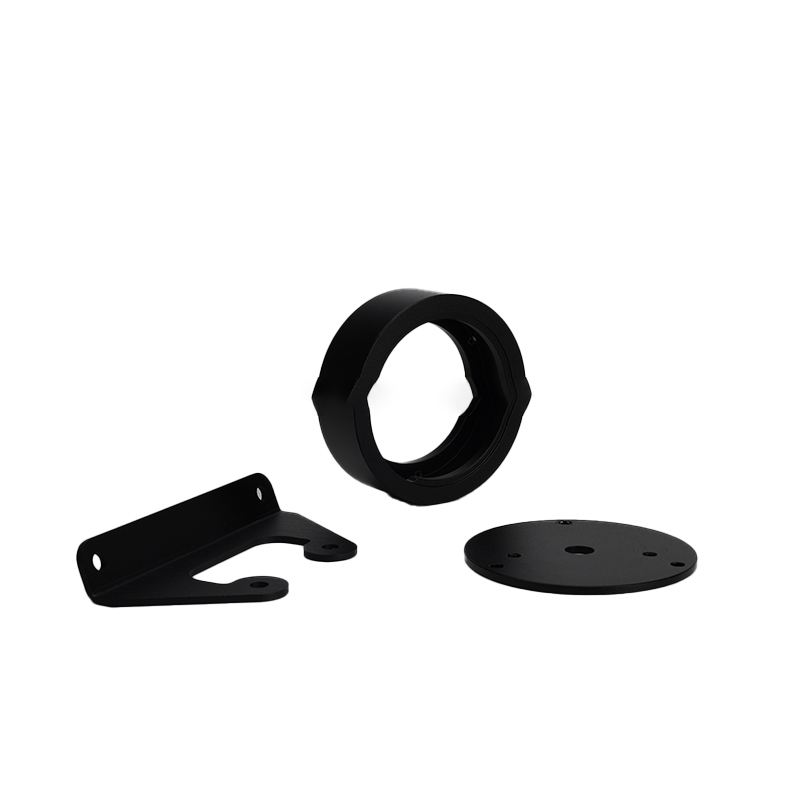
10.Ball Nose End Mills:
11.Advantages: Provide contouring ability and are well-suited for complex 3D shapes. They can also be used for finishing operations.
12.Application: Ideal for machining curved surfaces and sculpted profiles in aluminum.
13.Diamond-Coated Router Bits:
14.Advantages: Diamond coating provides excellent wear resistance and durability when machining abrasive materials like aluminum.
15.Application: Used for engraving, V-grooving, and other precision operations in aluminum.
CNC Projects in Aluminum
16.Prototyping and Production Parts:
17.CNC machining is widely used for manufacturing prototypes and production parts in industries ranging from aerospace to automotive due to its precision and repeatability.
18.Enclosures and Panels:
19.Aluminum is commonly used for manufacturing enclosures, chassis, and panels due to its lightweight yet sturdy nature.
20.Heat Sinks:
21.CNC machining allows for intricate designs and precise dimensions needed for effective heat sink solutions in electronics and thermal management applications.
22.Custom Components:
23.CNC machines can produce custom aluminum components such as brackets, mounts, and fittings tailored to specific industrial or consumer applications.
24.Art and Decorative Items:
25.Aluminum’s versatility allows for the creation of intricate art pieces, sculptures, and decorative items through CNC machining.
26.Jigs and Fixtures:
27.Aluminum jigs and fixtures are used in manufacturing processes to hold workpieces in place, ensuring accuracy and repeatability during machining operations.
Considerations for CNC Machining Aluminum
28.Chip Evacuation: Aluminum chips can be sticky and cling to tools. Proper chip evacuation is crucial to prevent chip buildup and tool wear.
29.Cutting Speeds and Feeds: Optimizing cutting speeds and feeds is essential for efficient machining of aluminum while avoiding tool deflection and surface roughness.
30.Coolant and Lubrication: Using appropriate coolant or lubricant helps dissipate heat and prolong tool life during aluminum machining operations.
By selecting the right CNC router bits and designing projects that leverage aluminum’s properties, you can achieve precise, high-quality results suitable for a wide range of applications. Whether you’re machining prototypes, functional components, or artistic creations, aluminum’s versatility and CNC machining capabilities offer ample opportunities for creativity and precision.