Mold release agents are crucial in the plastic molding process to facilitate the easy removal of molded parts from the mold cavity. These agents prevent adhesion between the molded part and the mold surface, allowing for smooth release without damaging the part or the mold. Here’s a breakdown of mold release agents for plastic molds:
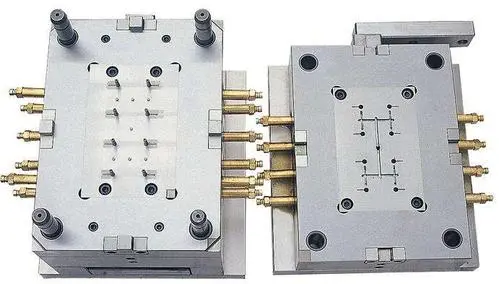
1.Types of Mold Release Agents:
2.Liquid Release Agents: These are typically applied as a spray, brush-on, or wipe-on application. They form a thin film between the mold surface and the molded part, providing easy release. Liquid release agents can be solvent-based or water-based.
3.Semi-Permanent Release Agents: These are more durable than liquid release agents and can withstand multiple molding cycles before reapplication is needed. They are usually applied as a thin film and chemically bond to the mold surface, providing excellent release properties.
4.Dry Film Release Agents: These are applied as a dry powder or aerosol spray and form a thin, dry film on the mold surface. Dry film release agents provide good release properties and can be suitable for high-temperature molding processes.
5.Selection Criteria:
6.Compatibility: The mold release agent should be compatible with both the mold material and the plastic resin being used for molding. Compatibility ensures proper adhesion and effectiveness of the release agent.
7.Temperature Resistance: Consider the temperature requirements of the molding process, as some release agents may degrade or lose effectiveness at high temperatures.
8.Ease of Application: Choose a release agent that is easy to apply and does not require extensive preparation or cleanup.
9.Safety and Environmental Considerations: Ensure that the chosen release agent is safe to use and complies with relevant safety and environmental regulations.
10.Application Process:
11.Clean the mold surface thoroughly to remove any residues or contaminants.
12.Apply the release agent evenly to the mold surface, ensuring complete coverage.
13.Allow the release agent to dry or cure according to the manufacturer’s instructions before beginning the molding process.
14.Reapply the release agent as needed, especially after prolonged use or if the molded parts start sticking to the mold surface.
15.Maintenance and Cleaning:
16.Regularly clean the mold surface to remove any buildup of release agent residues, dirt, or debris.
17.Inspect the mold for any signs of wear or damage to ensure proper release and part quality.
18.Follow proper storage and handling procedures for the release agent to maintain its effectiveness and shelf life.
By selecting the appropriate mold release agent and following proper application and maintenance procedures, manufacturers can optimize the plastic molding process and ensure consistent production of high-quality molded parts.
Mould Material | P20/718/738/NAK80/S136/2738/2316/H13, etc. |
Moud Precision | +/-0.01mm |
Equipment | CNC,EDM, Wire Cutting Machine, grinding ,drilling ,injection machine |