Certainly! Here’s an overview of custom prototype model making and the rapid prototyping process:
Custom Prototype Model Makers:
1.Services Offered: Prototype model makers specialize in creating custom prototypes based on client specifications. They typically work with a variety of materials such as plastics, metals (including aluminum), and composites.
2.Capabilities:
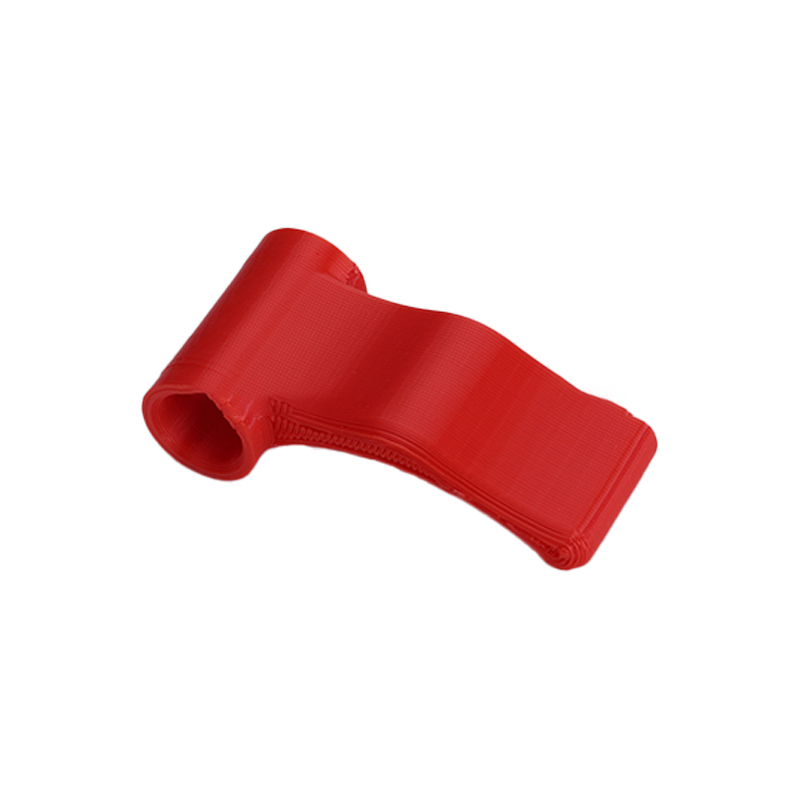
3.CAD Design: They can work from your CAD files or assist in creating them if needed.
4.Material Selection: Based on the prototype’s function, they advise on suitable materials and manufacturing methods.
5.Prototyping Techniques: Utilize various techniques such as 3D printing, CNC machining, vacuum casting, and rapid tooling.
6.Customization: Prototype makers offer flexibility in design iterations and can produce prototypes for different stages of product development, from concept validation to functional testing.
7.Quality and Precision: Experienced prototype makers ensure high precision and quality control throughout the manufacturing process to meet client expectations.
Rapid Prototyping Process:
Rapid prototyping involves several stages, depending on the chosen technique:
8.Design: Start with a CAD model of the prototype. This model serves as the blueprint for manufacturing.
9.Prototype Manufacturing:
10.3D Printing: Additive manufacturing technique that builds prototypes layer by layer from CAD data. Suitable for complex geometries and quick iterations.
11.CNC Machining: Subtractive manufacturing process where a block of material (e.g., aluminum) is cut away to create the prototype based on the CAD model. Offers high precision and a range of material options.
12.Vacuum Casting: Uses a master model to create multiple copies of the prototype using silicone molds and casting resins. Ideal for small-batch production and achieving end-use material properties.
13.Finishing: Post-processing steps like sanding, painting, or assembly are performed to achieve the desired look and functionality.
14.Testing and Iteration: The prototype undergoes testing to validate design and functionality. Iterations may be made based on test results and client feedback.
15.Production Readiness: Once the prototype meets all requirements, it can serve as a basis for scaling up to full production, using traditional manufacturing methods.
Benefits of Rapid Prototyping:
16.Speed: Quickly produce prototypes for testing and validation.
17.Cost-Effectiveness: Reduces tooling costs and allows for design adjustments early in the process.
18.Flexibility: Supports iterative design improvements and customization.
19.Risk Reduction: Identifies design flaws and manufacturing challenges early, reducing overall project risk.
Choosing the right prototyping method depends on factors like budget, timeline, material requirements, and the complexity of the design. Experienced prototype makers can guide you through this process and recommend the best approach for your specific needs.
If you have more questions or need further details on any aspect, feel free to ask!